Quartz torches are essential components of ICP instruments, but they also require proper care and handling to ensure optimal performance and longevity. In this article on Devitrification and Solarization, we share insights from Precision Glassblowing, a leading manufacturer of high-quality glassware for analytical chemistry.

The Dual Nature of Quartz
Quartz is a type of glass that is made from silicon dioxide (SiO2). It has excellent optical, thermal, and chemical properties, making it ideal for ICP applications. However, quartz also has some drawbacks, such as devitrification and solarization, which can affect its quality and durability.
How Quartz is Created
Regardless of the supplier, all fused quartz used in ICP glassware (no matter the manufacturer) begins life as sand, the majority of which is mined by the Unimin Corporation.
The sand is heated to an extremely hot temperature until it melts and becomes molten quartz. There are two main methods of making quartz tubing, rods, and plate: electric fusion and flame fusion.
Electric fusion involves heating the sand in an electrically heated crucible on top of a five-story tower. As the molten quartz exits the crucible, it travels through a hole and around a pin of specific dimensions, resulting in tubing of the desired size and tolerance. Most quartz used by Precision Glassblowing is made using the electric fusion process.
Flame fusion involves introducing the sand into a hydrogen/oxygen flame. The sand melts and collects on a rod that is removed from the flame, slowly, resulting in a solid quartz ingot. Precision Glassblowing uses high-quality quartz that is produced using a three-step process, resulting in quartz tubing with consistent dimensions and excellent clarity.
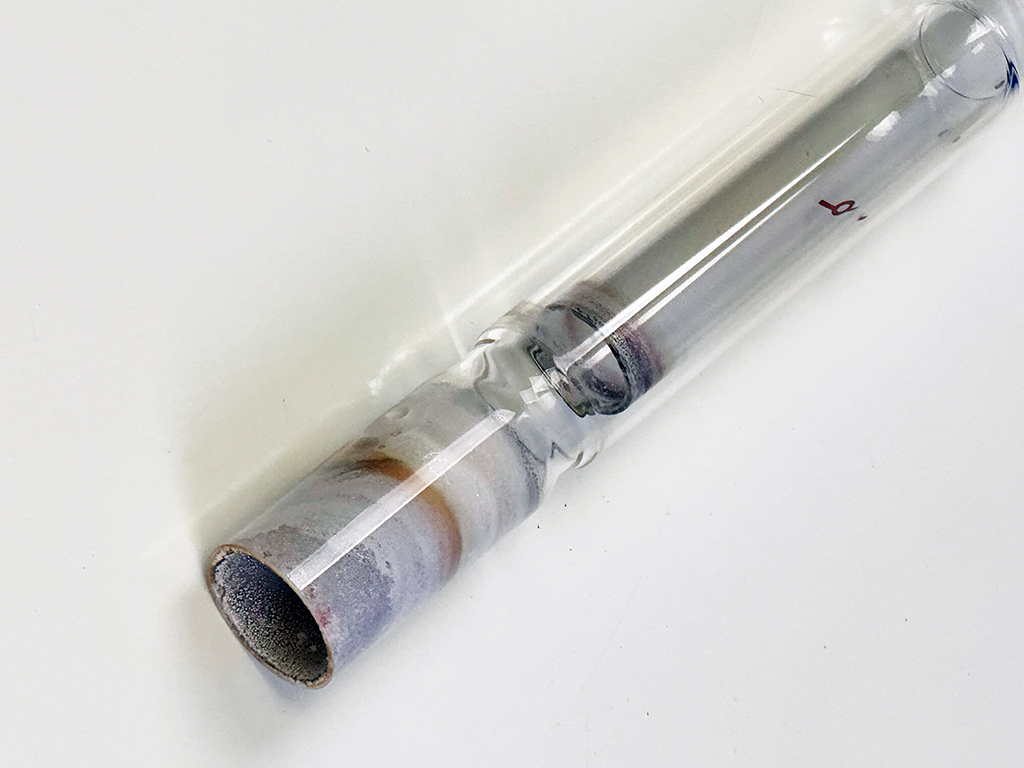
What is Devitrification?
Devitrification is the process of quartz atoms rearranging themselves into an orderly, crystalline structure. Quartz only exists as a smooth, clear material because the atoms have difficulty forming a regular pattern before the molten material cools into a solid. Devitrification can affect the optical properties of the quartz, cause it to lose its glassy structure, and increase the risk of cracking or breaking.
Devitrification is caused primarily by two factors: contamination and atmosphere. Contamination refers to the introduction of alkali elements such as sodium, potassium, or lithium to the quartz. These elements can come from the oils present in the skin or from water drops that attract contaminants. Contamination can promote devitrification when combined with heat, specifically 1000 degrees C or higher.
The atmosphere also has an impact on devitrification. Quartz is manufactured in a partial vacuum and has an oxygen deficit. To re-crystallize, quartz requires a more perfect ratio of silicon to oxygen (1:2). Since the atmosphere contains oxygen, there is always some oxygen present to promote devitrification. Adding more oxygen or increasing the temperature can speed up the devitrification process.
What is Solarization?
Solarization is another form of devitrification that occurs when quartz is exposed to deep ultraviolet (UV) radiation in a high-temperature environment. This can happen when running organics at high power settings on ICP instruments.
Solarization occurs because quartz contains microscopic impurities, such as metals, which absorb UV energy and cause localized devitrification at these sites. This devitrified glass has a different thermal expansion coefficient than the surrounding glass and leads to microscopic stress cracks as the torch is heated and cooled. These cracks can weaken the torch and cause it to fail.
How to Prevent Devitrification and Solarization
Preventing Devitrification
The best way to prevent devitrification is to avoid contamination and exposure to high temperatures and oxygen. Here are some tips from Precision Glassblowing:
• Never touch the outer shield of an ICP torch with your bare hand. Always wear cotton or latex gloves when handling quartz products.
• Do not rinse a dirty torch in water, detergent, or acid solution. This may cause thermal shock and breakage due to the heating and cooling cycle inherent to ICP operation.
• Avoid cleaning your torches unless necessary. Cleaning can do more harm than good by introducing solvents or stress to the quartz.
• If you must clean your torch due to inferior performance, bake it in a muffle furnace at 500 C for 30 minutes, followed by a simple rinse with DI water (15 megohm or greater). This is the best way to remove any deposits or contaminants without damaging the quartz structure.
• Consider switching to a torch that incorporates unconventional materials for the outer shield if you are running applications that are prone to devitrification. Some OEMs offer an ‘organics’ torch that has an outer shield made from quartz that resists devitrification. This tubing is more expensive than standard quartz tubing but may last longer and save you money over time.
• If your torch breaks or cracks, you may be able to repair it instead of buying a new one. Precision Glassblowing offers a repair service for quartz torches that can restore them to their original condition. Repairing is a cost-effective option that can extend the life of your torch and reduce waste.
Preventing Solarization
Solarization is a natural and inevitable result of operating torches under the conditions inherent in organics. However, there are some ways to slow down the process and extend the life of your torch:
• Avoid cleaning your torches unless necessary. Cleaning can introduce hydrogen to the quartz, which can bond with the broken bonds in the SiO2 caused by solarization and amplify the internal stress.
• Consider switching to a torch that incorporates unconventional materials for the outer shield if you are running applications that are prone to solarization. Some OEMs offer an ‘organic’ torch that has an outer shield made from quartz that resists solarization. This tubing is more expensive than standard quartz tubing but may last longer and save you money over time.
• If your torch breaks or cracks, you may be able to repair it instead of buying a new one. Precision Glassblowing offers a repair service for quartz torches that can restore them to their original condition. Repairing is a cost-effective option that can extend the life of your torch and reduce waste.

Trust Precision Glassblowing
Precision Glassblowing is committed to providing the highest quality glassware available for analytical chemistry applications. We use only the best quartz and borosilicate materials and never compromise our quality standards for the sake of saving a few dollars. Our dedicated R&D staff and glassblowers are constantly researching new production methods, ensuring that our quality remains among the highest in the industry.
When you buy glassware from Precision Glassblowing, you can be sure that you are getting the best product for your instrument. Check with your glassware distributor to make sure that you are receiving Precision Glassblowing glassware. For additional information about our quality standards, materials, or product information, please call or email.